Praxisbericht 3D-Drucker
im Einsatz für Modellgusskonstruktionen mit Teleskopen
Interview mit ZTM Ulrich Schloh, Fertigungsleiter der CAD/CAM-Abteilung im Suter Dental Labor in Bremervörde. Ulrich Schloh nutzt für die Prozessoptimierung der Modellgusskonstruktionen den BEGO Varseo 3D-Drucker, die dazugehörigen Materialien und die eigens entwickelte Softwarelösung.
Herr Schloh, wie ist das Suter Dental Labor zum 3D-Druck gekommen und worin sehen Sie die Vorteile für Ihr Labor?
Ulrich Schloh: Wir haben die Marktentwicklung der 3D-Drucker für die Dentalbranche aufmerksam beobachtet und die Vorteile für unser Labor herausgearbeitet. Im vergangenen Jahr konnten wir unseren Manufakturbetrieb erfreulicherweise mit der innovativen Technologie des BEGO 3D-Druckers Varseo erweitern. Diese Ergänzung bringt uns auch in unserem regionalen Markt in eine Poleposition der modernen Produktionsverfahren und unterstreicht unser Know How für die Dentaltechnik. Wir Mitarbeiter schätzen Investitionen in den Maschinenpark und in perfekte Arbeitsplatzbedingungen und sehen es als Sicherung für die Zukunft.
Welche Fragen haben Sie sich vor der Aufstellung des 3D-Druckers gestellt?
Ulrich Schloh: Vor der Aufstellung haben wir uns gründlich Gedanken über die Prozesswege und einen optimalen Maschinenplatz gemacht. Wir haben diese Gelegenheit genutzt, unsere Abläufe im digitalen Workflow zu überdenken und zu optimieren. Daraus folgte eine gezielte Umstrukturierung der Arbeitsräume. In unserer Designabteilung haben wir jetzt bis zu acht Arbeitsplätze, an denen digital gearbeitet und konstruiert werden kann. Diese Abteilung ist räumlich getrennt von den weiteren Laborräumen. Der 3D-Drucker befindet sich ebenfalls in der neuen Designabteilung und kann in direktem Kontakt zu den Konstruktionsplätzen bedient und bestückt werden.
Wie verliefen Aufstellung und Inbetriebnahme des Druckers?
Ulrich Schloh: Die Aufstellung und Inbetriebnahme des Varseo 3D-Druckers waren unkompliziert. Mit dem BEGO Medical Außendienstmitarbeiter Stefan Knade erfolgte eine fachliche Einführung und Materialschulung. So konnten wir den Drucker direkt in den Arbeitsalltag nutzbringend integrieren und bereits am nächsten Tag Modellgusskonstruktionen im 3D-Druckverfahren herstellen und gießen. Dieser Produktionsschritt ergänzt unser Ziel, auch Gusskonstruktionen digitalisiert zu fertigen.
Wir arbeiten im Suter Dental Labor seit Langem routiniert im CAD/CAM-Verfahren. Die Erweiterung um den 3D-Druck kam genau zum richtigen Zeitpunkt und ist ein logischer Anschluss an die digitalen Produktionsprozesse.
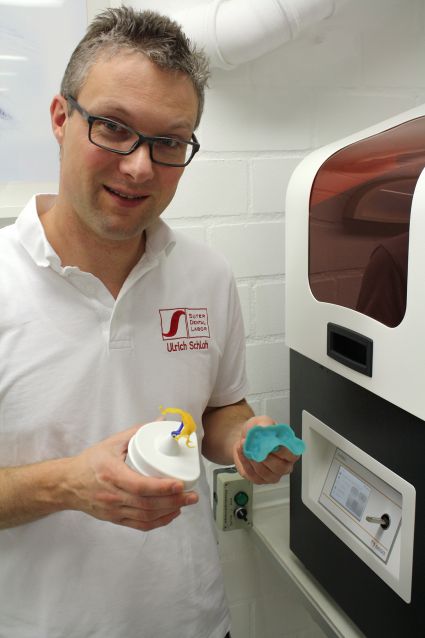
ZTM Ulrich Schloh mit dem BEGO Varseo
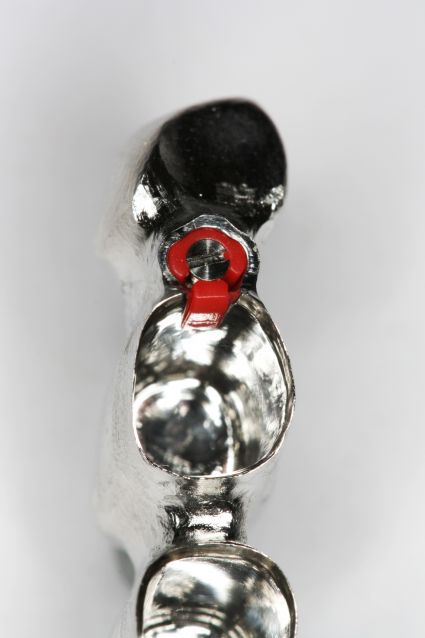
Aktivierbares Friktionselement
Sie haben von der digitalen Fertigung von Modellgusskonstruktionen gesprochen. Wo genau sehen Sie hier die Vorteile?
Ulrich Schloh: Selbstverständlich war es unser Wunsch, die Teleskoptechnik in den digitalen Workflow zu integrieren. Viele Zahnärzte schätzen seit Jahren die aktivierbaren Friktionselemente. Diese Technik gewährt eine dauerhafte Aktivierung und ermöglicht eine individuelle Anpassung an den Friktionswunsch des Patienten. Eine besondere Herausforderung war jedoch die Verbindung von gefrästen Primär- und Sekundärteleskopen mit Friktionselementen. Es war eine wirkliche Missionsaufgabe, da es bislang keine Softwarelösung zur Umsetzung von digital erstellten aktivierbaren Friktionselementen gab. Mittlerweile bieten aber viele Hersteller diese Möglichkeit an.
Die Herstellung dieser Technik erfordert den Einsatz einer Kombination aus optischen und taktilen Scannern. Hier haben wir uns für die Systeme von 3Shape und Renishaw entschieden. Zunächst mussten wir einigen Pioniergeist aufbringen, um Datensätze für die Friktionselemente zu erstellen. Mittlerweile ist dies ein routinierter Vorgang, bei dem wir die Friktionselemente als Platzhalter in die Konstruktionen in der Software matchen. Durch die räumlich enge Verbindung zwischen Konstruktion und Fräsmaschinen kann ein unmittelbarer Einfluss auf die Fräsergebnisse erfolgen. Der Verlauf der Fräserstandzeit wird feinjustiert und wir erreichen hiermit ein perfektes Passungsverhältnis. In der Verbindung von Teleskoptechnik zu Modellgussplatten unterbrach bisher lediglich die herkömmliche Herstellung der Modellgüsse den digitalisierten Arbeitsablauf. Um die Fertigungsplanung auch noch durch das Designen der Modellgusselemente zu ergänzen, haben wir uns zum Ziel gesetzt, die Herstellung von Teleskoparbeiten durch die Verwendung von gedruckten Modellgusselementen zu kombinieren. Dieses Ziel haben wir Anfang 2016 erreicht und jetzt können wir den gesamten digitalen Designprozess nutzen.
Ein großer Vorteil ist, dass wir die gesamte Sekundärkonstruktion mit nur einem Scan durchführen können. Dies ist zeiteffizient und spart Materialkosten. Im Vergleich zur analogen Modellgussherstellung werden Doubliersilikon und die Hälfte der Einbettmasse eingespart.
Beschreiben Sie uns doch einmal das besondere Vorgehen des Designens für den Modellguss.
Ulrich Schloh: Sofern die virtuelle Konstruktion der Sekundärteile abgeschlossen ist, kann diese anschließend mit dem Modellscan zusammengeführt werden. Hierfür ist ein besonderes Kopieren vorgesehen. Dafür wird im 3Shape Konstruktionsprogramm im Auftragsblatt die fertige Konstruktion markiert. Mit der rechten Maustaste öffnet sich per Klick ein Dropdownfenster, dass den Befehl enthält: „Konstruktion kopieren und an den Präparationsscan anhängen“. Durch diesen Vorgang werden die Sekundärteile mit dem Modellscan verschmolzen. Hierfür ist es notwendig, diesen Auftrag in einen Modellgussauftrag umzuwandeln. Anschließend kann das Design des Modellgusselementes erfolgen.
Wo sehen Sie weitere Vorteile in der Umsetzung eines kompletten digitalen Workflows?
Ulrich Schloh: Ein weiterer Vorteil liegt in der parallelen Fertigung von Sekundärkronen und Modellgussgerüst. Während der Fräsauftrag der Teleskope erfolgt, wird das Gerüst bereits am Varseo 3D-Drucker hergestellt. Hieraus ergibt sich wieder ein Zeitvorteil und ein flexibler Workflow. Bei einer zu hohen internen Auslastung und speziellen Aufträgen greifen wir auf die Zentralfertigung im Bremer CAD/CAM-Produktionszentrum der BEGO Medical zurück.
Dort stehen uns auch für die Teleskop- bzw. Doppelkronentechnik verschiedene Fertigungsverfahren und Materialien zur Auswahl.
Wie erfolgt die Datenübertragung vom Rechner zum Varseo?
Ulrich Schloh: Jeder Druckauftrag wird zur Zeit einzeln per USB-Stick an das Gerät übertragen und ist nicht ans Netzwerk angeschlossen. Dieses Vorgehen hat aus unserer Sicht einen deutlichen Vorteil: Im Falle eines Fehlgusses kann man sehr rasch einen Druckauftrag wiederholen, ohne dass man noch einmal am Rechner die Konstruktionsdaten auffinden und auslösen muss. Aus diesem Grund verbleibt der USB-Stick bei der Arbeitsschale.
Wie lange dauert der Druck eines Modellgusses in der Regel und welche Schritte sind anschließend
in der Nachbearbeitung nötig?
Ulrich Schloh: Der Varseo 3D-Drucker bietet eine Bauplattengröße von 96 x 54 mm und eine Bauhöhe von 85 mm. Diese Fläche reicht selbstverständlich für die herkömmlichen Modellgussplatten aus. Für den Druck der Modellgusselemente wird das VarseoWax CAD/Cast Spezialharz verwendet. Nach etwa 75 Minuten ist der Druckvorgang des Modellgussgerüsts beendet. Die Kartusche wird anschließend aus dem Gerät entnommen. Das Objekt wird vom Druckstempel abgelöst und in einem Ultraschallbad mit Ethanol gereinigt. Anschließend werden die Supportverbindungen zwischen Bauplatte und Druckobjekt mit einer feinen Zange abgeknippst.
Die überschüssigen Supports werden einfach weggebrochen und ggf. leicht verschlichtet. Das Modellgusselement kann jetzt auf Passung am Gipsmodel überprüft und nachgehärtet werden.
Welche Einbettmasse verwenden Sie im Zusammenhang mit Konstruktionen aus dem
3D-Drucker?
Ulrich Schloh: Beim Gießen der Modellgusskonstruktionen haben wir Versuche mit verschiedenen Einbettmassen durchgeführt. Bei einigen Materialien gab es Reaktionen mit dem gedruckten Kunststoffmaterial. In der Verbindung mit der empfohlenen BEGO Einbettmasse VarseoVest P ließen sich jedoch optimale Ergebnisse erzielen. Hier ist die Verwendung der Systemmaterialien zielführend. Für die Erreichung von optimalen Gussergebnissen sind die Herstellerangaben zu den Gussparametern zu beachten.
Nach dem Guss haben wir festgestellt, dass sich die Oberflächenstruktur von der gewohnten klassischen Wachsmethode unterscheidet und rauher erscheint. Nach einem kurzen Politurvorgang errreichen wir aber eine angenehme Oberflächenoptik und das weitere Vorgehen erfolgt wie im gewohnten analogen Herstellungsverfahren.
Wie leicht fiel Ihnen der Einstieg in die 3D-Druck ,Technologie?
Ulrich Schloh: Die 3D-Druck Technologie ist für den Zahntechniker ein neues und spannendes Innovationsfeld. Wir haben sehr von den speziellen Anwenderkursen des Herstellers BEGO profitiert. Für Interessierte und Einsteiger wird ein 3D-Druck Schnupperkurs angeboten. Neben Informationen zu den verschiedenen Seminarangeboten findet man auf der Herstellerseite diverse hilfreiche Informationen rund um den 3D-Druck – auch in Form von Videotutorials oder FAQ. Vor allem haben uns aber die gute Betreuung und Beratung durch den Außendienst sehr beim Start geholfen. Der Einstieg gelang damit relativ leicht und schnell.
Was sind Ihre nächsten Schritte im digitalen Workflow?
Ulrich Schloh: Die Entwicklung der Materialien für den Einsatz an Patientenarbeiten hat noch große Potenziale. Hier ist noch einiges zu erwarten. Als nächstes werden wir Implantatübertragungsschlüssel gefertigt aus dem Spezialharz VarseoWax Surgical Guide anbieten. Das Design des Übertragungsschlüssels erfolgt auf demselben Datensatz des Abutmentdesigns und wird in einem gemeinsamen Arbeitsschritt konstruiert. Es wird anschließend parallel zur Abutmentherstellung zeitgleich gedruckt. Der Übertragungsschlüssel bietet eine direkte Unterstützung bei der Eingliederung von Implantatabutments am Patienten. Dies bringt einen spürbaren Nutzen für den behandelnden Zahnarzt im Praxisalltag.
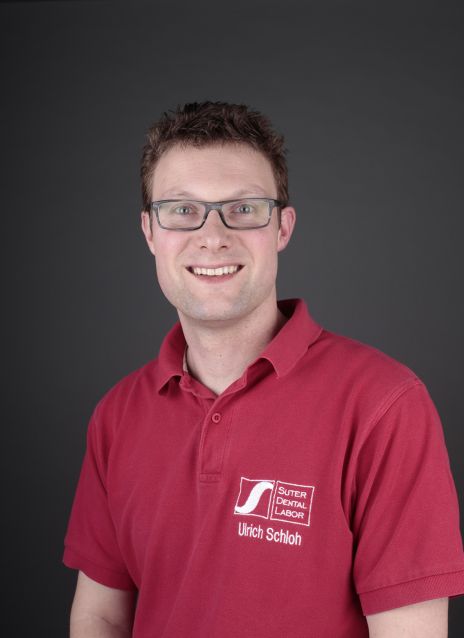
Zahntechnikermeister Ulrich Schloh
TK-Soft Friktionslement bietet überzeugend Merkmale: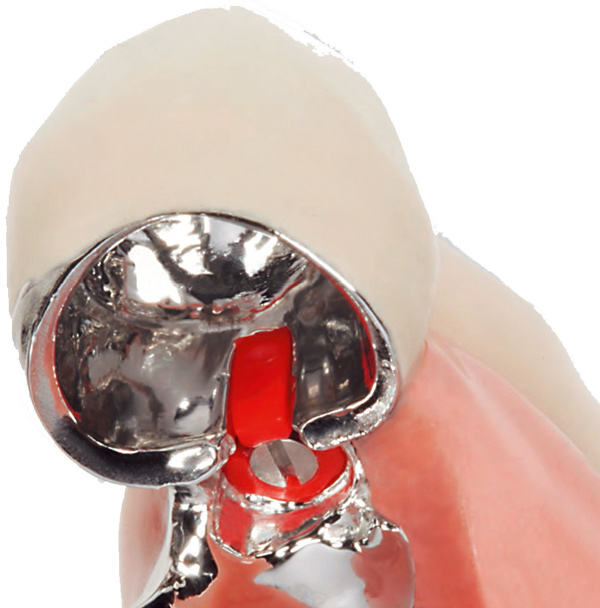
Vorteile
- Gewährleistung einer dauerhaften Aktivierung durch integrierte Metallverschraubung
- Verschleißfester Kunststoff
- Langlebig durch Titangewinde
- Stufenlos einstellbar
- Individuelle Anpassung an den Friktionswunsch des Patienten
Bei herkömmlichen Friktionsteilen wird die Schraube in das Kunststoff teil gedreht. Problem: bei Aktivierung kann die Schraube durchdrehen bzw. ausreißen, weil der Kunststoff nachgibt. Dank integrierter Kontermutter aus Titan kann dies beim TK-Soft® nicht passieren! Hier wird die Aktivierschraube von einer Titanmutter gekontert. Die Haltekraft der Prothese kann damit sehr fein stufenlos reguliert und immer wieder nachaktiviert werden.